Failure mode and effects analysis (FMEA) is widely used in the development and manufacturing industries to eliminate or minimise potential failure mechanisms and improve successful operation and safety. By reviewing as many components, assemblies and subsystems to identify potential failures and their impacts, engineers can examine systems' reliability. Recorded FMEA data makes it easy to develop a Quality Management System (QMS) and carry out risk-based thinking required by IATF 16949 [1].
Four Types of FMEA
There are four types of FMEA based on a stage of product development cycles [2].
- Functional: before design solutions are provided, the method can be used to figure out potential functional failure effects.
- Concept design/hardware: In the early design concept stages, this analysis can be useful to check the failure mechanisms or lower-level functional failures.
- Detailed design/hardware: prior to the production stage, this analysis can analyse any possible failures. This process is the most detailed process, so full analysis is performed, such as any failure effect severity, failure prevention, failure detection and diagnostics.
- Process: This analysis is used to identify errors in manufacturing and assembly processes.
FMEA Worksheet and How To Calculate a Risk Level
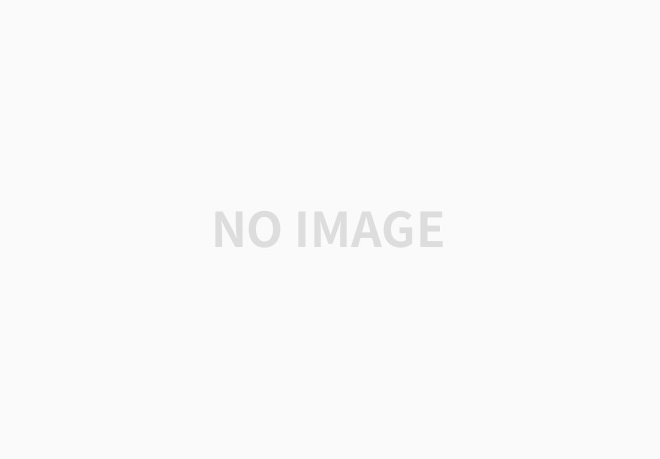
The FMEA is created within a worksheet like the table above (figure 1). The analysis process is started by listing the functions of the system.
An FMEA uses three criteria to access problems and calculate a risk level [2].
- Probability (P): define the probability of failure occurrences during the expected lifetime of the product/system. The level of probability can be defined from 'extremely unlikely (rating 1)' to 'frequent (rating 5)'.
- Severity (S): determine the severity of end effects in terms of what the users (industry, company or customers) might see or experience. Each end effect element is defined from 'no effect (rating 1)' to 'catastrophic (rating 5)'.
- Detection (D): define the probability of the failure being detected by the operator or maintainers. it can be ranked from 'certain (rating 1)' to 'Undetected (rating 6)'
Based on the above values, the Risk Priority Number (RPN) can be calculated. Note that the RPN can be used for comparison within one process only. Crossing comparisons between different processes or organizations are not eligible [4]. By multiplying P, S and D ratings, FMEA RPN can be calculated.
Risk Priority Number (RPN) = Probability (P) × Severity (S) × Detection (D)
The RPN is used to prioritise high-risk problems and determine appropriate actions. However, the RPN values do not directly indicate a high risk for the system. For example, two different failure modes can have the same RPN values, but the rank of severity can be significantly different. Therefore some companies combine the RPN values and severity ranks, for instance, risk matrix (priority matrix) (figure 2).
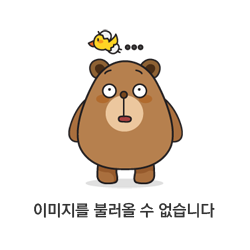
Advantages and Limitations
The benefits of FMEA are clear. The process can detect potential failures in the early development stage and eliminate the issues. It will reduce potential associated costs and directly impact to company's profit. The quality, reliability and safety of a system/product will be improved [2].
While the FMEA process prevents potential problems, the process is complicated to read, understand, maintain and also a highly time-consuming process [2, 5-6]. In addition, as discussed in the limitation of the RPN method, to indicate correct action, various solutions need to be used such as a risk matrix.
Nevertheless, FMEA is widely used in various industries to evaluate potential risks due to its clear advantages.
[References]
'Technology > Manufacturing Engineering' 카테고리의 다른 글
Process Capability Index: Cp, Cpk (0) | 2022.08.15 |
---|---|
Lean Manufacturing (0) | 2022.01.13 |
Six Types of Manufacturing Process (0) | 2022.01.08 |
List of Manufacturing Process (0) | 2022.01.06 |